Budgeting for Replacement Parts: What You Need to Know
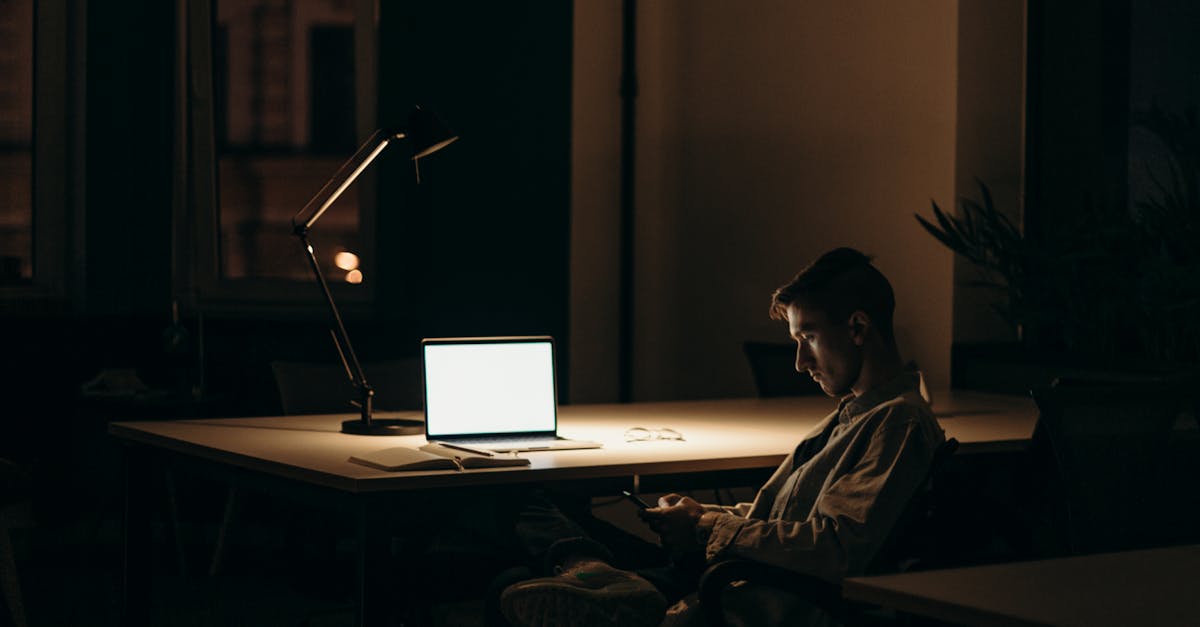
Table Of Contents
Building a Relationship with Suppliers
Creating strong relationships with suppliers can significantly impact the efficiency and effectiveness of your operations. Engaging regularly with suppliers fosters trust and encourages open communication. Establishing a rapport ensures that you are consistently updated on product availability, pricing changes, and upcoming innovations. This proactive approach also helps suppliers understand your specific needs, enabling them to offer tailored solutions that can enhance your budgeting practices.
A reliable supplier network can provide advantages like prioritised service during peak times and access to exclusive deals or discounts. When suppliers view you as a valued partner, they may be more willing to accommodate your requests or negotiate better pricing. This relationship not only caters to your immediate needs but also supports long-term sustainability by contributing to a stable supply chain.
Benefits of Establishing a Consistent Supplier Network
Building a reliable supplier network can significantly enhance operational efficiency. When you establish long-term relationships with suppliers, you often benefit from preferential pricing and access to better product quality. Suppliers familiar with your business requirements tend to offer more tailored solutions, which can lead to cost savings over time. This familiarity also fosters open communication, making it easier to negotiate terms and resolve issues swiftly.
Consistency in supplier selection contributes to better inventory management. When you work with the same suppliers, predicting lead times and stock availability becomes simpler. This predictability allows for more effective planning, reducing the chances of overstocking or stockouts. Suppliers invested in long-term partnerships may also provide insights into emerging trends and technologies, ensuring that your operations stay competitive.
Contingency Planning for Emergencies
Having a plan in place for unexpected failures can save both time and money. Preparing for emergencies involves more than just having a budget; it requires setting aside funds specifically designated for urgent needs. This emergency fund provides a financial buffer, ensuring that you can address unexpected costs without derailing other essential expenses. Consider the types of equipment or parts that frequently require replacement and allocate a portion of your budget accordingly.
Regularly reviewing and adjusting your contingency plan remains vital. As newer technologies emerge, the likelihood of needing replacement parts may increase or decrease. Staying aware of industry trends assists in making informed financial decisions. Tracking maintenance records and failure rates can also provide insights into which components might need additional allocations in the future. Adapting your strategy ensures you remain prepared, regardless of what challenges arise.
The Role of an Emergency Fund in Your Budget
An emergency fund plays a vital role in maintaining financial stability when unexpected costs arise. Having a designated amount set aside specifically for unforeseen circumstances allows businesses to address urgent replacement part needs without derailing their operational budget. This proactive approach not only eases the process of acquiring necessary components but also promotes overall confidence in managing day-to-day expenses.
Establishing an emergency fund involves careful planning and regular contributions to ensure that sufficient resources are available. It is essential to assess potential risks and costs associated with equipment failure or sudden repair needs. By factoring these possibilities into the budget, businesses can prepare for the unexpected and minimise the financial strain that might arise during challenging times.
Tracking and Managing Replacement Parts Inventory
Maintaining an accurate count of replacement parts is essential for seamless operations. A well-organised inventory system allows businesses to quickly identify what items are on hand and what needs to be ordered. Implementing barcode scanning or RFID technology streamlines this process, reducing the likelihood of human error while enhancing real-time tracking capabilities.
Regular audits of inventory are equally important in ensuring optimal stock levels. By developing a schedule for these audits, businesses can pinpoint slow-moving items and make informed decisions about purchasing practices. Utilising software that integrates inventory management with sales data can provide valuable insights, enabling organisations to adapt their strategies effectively while reducing waste and costs.
Tools and Techniques for Efficient Inventory Management
Effective inventory management is essential for maintaining optimal operations. Implementing a barcode system can streamline the process, allowing for quick tracking of parts as they enter and exit the inventory. This technique reduces manual errors and provides real-time updates on stock levels. Additionally, adopting inventory management software can enhance efficiency by automating reorder alerts and tracking usage patterns. An accurate digital record aids in decision-making, ensuring that necessary parts are always on hand.
Regular audits play a crucial role in managing replacement parts inventory. Conducting periodic reviews helps identify slow-moving items and allows for timely adjustments in purchasing strategies. Developing a systematic approach, such as FIFO (First In, First Out), ensures that older stock is used before it becomes obsolete. By incorporating these tools and techniques into inventory management practices, organisations can maximise their resources and improve overall productivity.
FAQS
Why is it important to build a relationship with suppliers for replacement parts?
Building a relationship with suppliers can lead to better pricing, reliable delivery times, and access to quality parts. It also fosters trust, which can be beneficial during emergencies or when negotiating terms.
What are the benefits of establishing a consistent supplier network?
A consistent supplier network ensures you have a reliable source for replacement parts, allows for bulk purchasing discounts, and helps you maintain quality control. It can also streamline the procurement process, saving time and money.
How can I effectively plan for emergencies in my budgeting for replacement parts?
Effective emergency planning involves setting aside a specific amount of your budget as an emergency fund, regularly reviewing your inventory levels, and establishing relationships with multiple suppliers to ensure you can quickly source parts when needed.
What role does an emergency fund play in my budget for replacement parts?
An emergency fund acts as a financial buffer that allows you to respond quickly to unexpected needs for replacement parts without disrupting your overall budget. It helps to reduce stress and ensures that you can maintain operations smoothly.
What tools and techniques can I use for efficient inventory management of replacement parts?
Various tools and techniques include inventory management software, barcoding systems, regular inventory audits, and implementing a just-in-time inventory approach. These methods help streamline tracking, reduce waste, and ensure you have the necessary parts on hand when needed.
Related Links
How to Source Affordable Screen Replacement ComponentsHidden Costs Associated with DIY Laptop Screen Repairs
Discounts and Offers for Laptop Screen Replacement Parts
Financial Planning for Unexpected Costs During Screen Replacement
Assessing DIY Repair Expenses: A Comprehensive Breakdown
Evaluating the Professional Help vs DIY Cost Factors
Comparing Prices: New vs Refurbished Laptop Screens